Latest News
CASE STUDY: Don’t give up on those older buildings! Energy efficient conversions and upgrades are still possible…
With the industry under the cosh for much of the post-Covid period, it is perhaps not surprising that growers have been forced into a defensive position when it comes to potato storage in recent seasons.
There are a few green shoots of recovery coming to light but, with new storage costs sky-rocketing to north of £400 per tonne. the focus for growers for now seems to be very clearly on directing any improvements towards what already exists rather than starting from the ground up.
An example of this approach provides a case study we visited recently. It is a store upgrade carried out this summer at Drayton Farms at Little Plumstead on the outskirts of Norwich, Norfolk by North Walsham-based suppliers Crop Systems Ltd. A pair of rather tired 1980s-built stores became the subject of an upgrade proposal with the objective of converting them to provide around 1500 tonnes of high quality, pre-pack storage.
The buildings themselves were metal-clad portal frame units with a modest amount of spray-foam insulation that was cosmetically damaged. Crop Systems proposal was to remove a central, non-structural dividing wall and a couple of existing fridges which were well past their use-by date. The installation would repair and renovate the spray-foam to provide around 85 – 90mm of good quality insulation across the newly-created, larger store. The doors were also a weak point in the store’s overall integrity, as is so often the case, so these were to be replaced with new Hormann up-and-over units with 40mm insulation.
Box stacking in older buildings can often be a challenge so this required some flexibility of thought but Drayton Farms gave the project the go-ahead based around the promise of close store control from the new SmartStor® controller and a state-of-the-art cooling and ventilation system designed and installed by Crop Systems’ directors, Ray Andrews and Richard Cook (right).
Boxes are stacked in a reworked but largely conventional format away from a full-width, but open-fronted, plenum chamber which allows the store to flex around a couple of differing box sizes on the production unit.
The store has an ambient, inverter-controlled drying system with full dew-point control to prevent condensation. The airflow is rated at ~0.03 m3/s/t (65 cfm/t) with the fans running flat out and that is at a nominal 150 Pa pressure. The store pairs the ‘free cooling’ option with a 90kW, glycol-based 4-compressor refrigeration unit which is fully speed-controlled. It is linked to a large, 6.4 metre wide refrigeration coil providing a big interface for efficient cooling to minimise weight loss. The indirect system uses around 600 litres of glycol (running at -2.6 to -3°C) but just a 16kg charge of refrigerant.
When PSI visited, the store had completed the drying/curing phase, when it was held at a target temperature of 8°C, and was in the process of pulling down to holding temperature. Pull-down rate was close to 1°C/day even with the system running at just 80% on the inverter, which offers a 50% reduction in power consumption compared with running at ‘full chat’.
Boxes are stacked in a reworked but largely conventional format away from a full-width, but open-fronted, plenum chamber which allows the store to flex around a couple of differing box sizes on the production unit.
The store has an ambient, inverter-controlled drying system with full dew-point control to prevent condensation. The airflow is rated at ~0.03 m3/s/t (65 cfm/t) with the fans running flat out and that is at a nominal 150 Pa pressure. The store pairs the ‘free cooling’ option with a 90kW, glycol-based 4-compressor refrigeration unit which is fully speed-controlled. It is linked to a large, 6.4 metre wide refrigeration coil providing a big interface for efficient cooling to minimise weight loss. The indirect system uses around 600 litres of glycol (running at -2.6 to -3°C) but just a 16kg charge of refrigerant.
When PSI visited, the store had completed the drying/curing phase, when it was held at a target temperature of 8°C, and was in the process of pulling down to holding temperature. Pull-down rate was close to 1°C/day even with the system running at just 80% on the inverter, which offers a 50% reduction in power consumption compared with running at ‘full chat’.
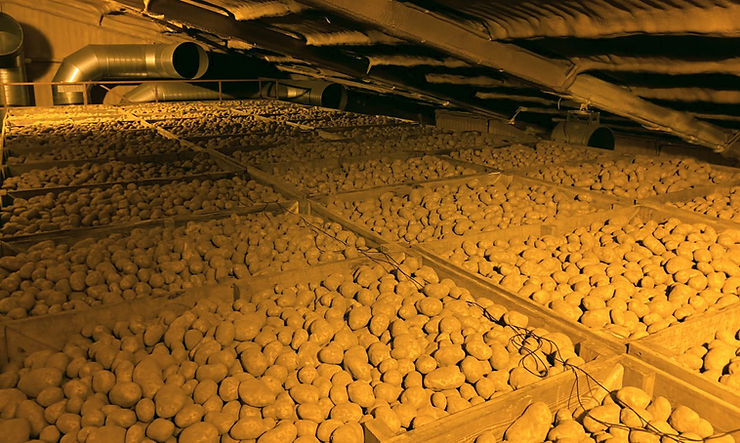
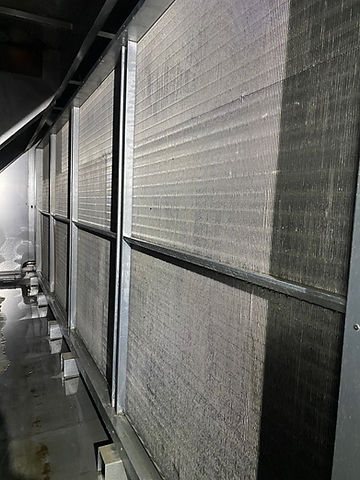
According to Mr Andrews, the modern design of the fully configurable system can reduce running costs by as much as 30%.
This is due to the combination of key design characteristics such as the high airflow, low back pressure and large fridge coil coupled with the ability to speed control all the key components.
A quick calculation using the consumption data instantly available on the SmartStor® control system showed drying and pull-down costs to be approximately £2.65 per tonne since loading on 28 September (to 18 Oct at 32p/kWh).
And, as far as the conversion costs go, Crop Systems estimate the cost of bringing this old store back to life at about £140/t.
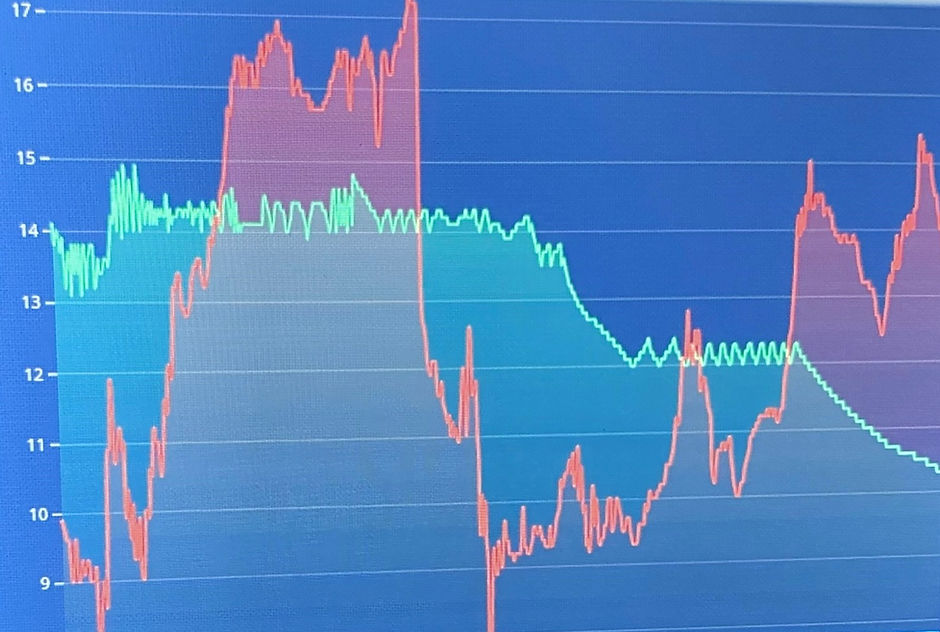
That figure includes the all-important controlunit which provides real-time information and data not only for the store conditions but also power use.
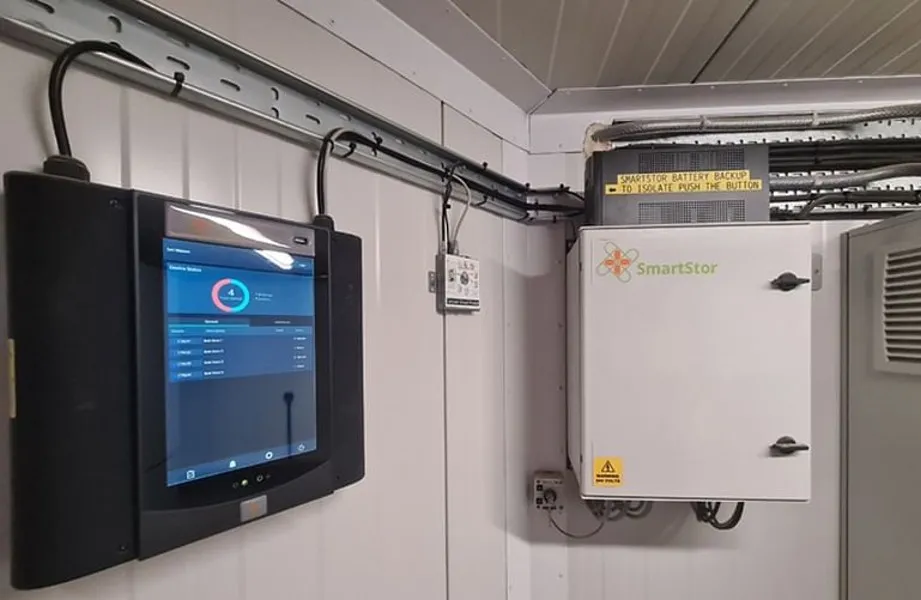
Green energy meets agriculture: Innovative ‘SmartSola’ system to revolutionize potato storage, cut electricity costs
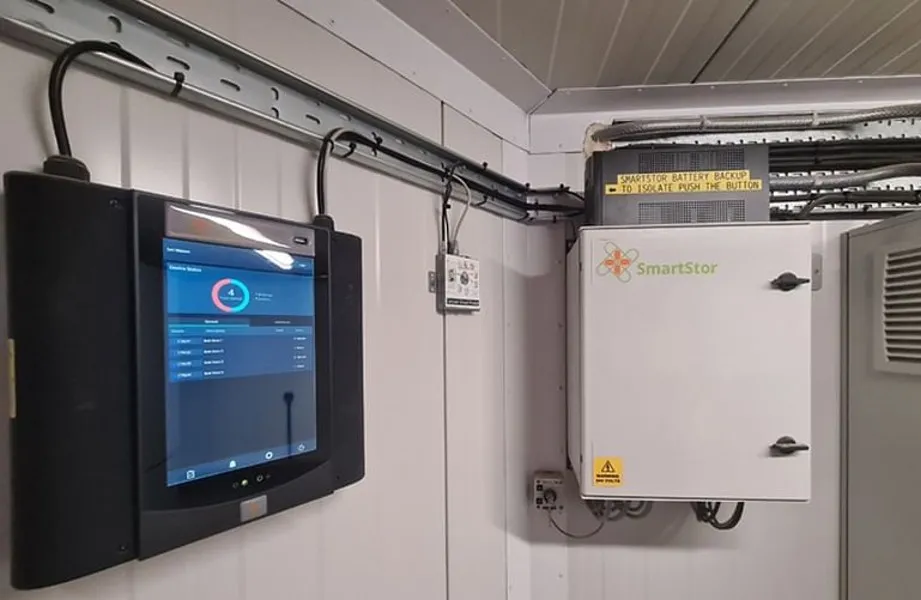
In a move that promises to reshape the landscape of energy storage for British potato operations, Crop Systems Limited, based in Norfolk, has unveiled its groundbreaking ‘SmartSola’ system. This timely innovation is set to be a game-changer for farmers looking to optimize their home-generated energy and cut back on external power costs.
The ‘SmartSola’ system is designed to monitor energy generated from a variety of sources, including solar, hydro, wind, and biomass. It then strategically deploys this energy across up to 10 storage facilities, ensuring optimal use and efficiency.
Stored crops maintained in pristine condition
Philip Smith, a proud owner of Monkton Court Farm located near Ramsgate in Kent, has been an early adopter of the ‘SmartSola’ system. He has integrated it across his 3,500-tonne storage facilities constructed by Crop Systems Limited.
Over the past five years, these facilities have maintained his potato crops in pristine ‘just harvested’ condition. This has been achieved with the aid of advanced equipment like glycol fridges, which ensure low running costs.
Smith is particularly impressed with the enhancements brought about by ‘SmartSola’. He shared, “Annually, our four storage facilities consume around 300,000 kWh of electricity. Given the skyrocketing energy costs, it’s imperative for us to maximize our home-produced solar energy.”
Smart control, coupled with adaptability
He further elaborated on the system’s benefits: “SmartSola has been instrumental in smartly controlling our storage run times. As solar energy becomes available, the system sequentially activates the stores. On numerous occasions, our storage facilities operate solely on energy from our solar panels, eliminating the need for external energy and its associated costs.”
Smith also highlighted the system’s adaptability, “We typically store our crops at 2.7°C with a 0.2°C differential. However, when there’s ample power from the solar panels, we can over-cool to 2.5°C. This means that on days when the panels aren’t as effective, we can bypass using mains electricity. The energy required is essentially stored within the potatoes themselves.”
He concluded by praising the system’s flexibility, saying “The program allows store managers to prioritize different storage facilities or set unique parameters for each. For us, ‘Smart Sola’ has proven invaluable in our storage management.”
This innovative approach by Crop Systems Limited is a testament to the potential of harnessing home-generated energy, offering a sustainable and cost-effective solution for potato farmers across the UK.

Here at Crop Systems we are very excited to launch SmartSola™
SmartSola™ is a new software program that looks at the power needed to run a store and, if that power is available from a renewable source, like solar or wind, utilises that power in preference to it being exported to the grind.
This maximises the use of cheap renewable energy to power the stores and will work on up to 10 stores on site, prioritising certain stores if necessary.
SmartSola™ operates with other Crop Systems software and equipment, like SmartStor™, as part of an integrated control suite to give you not just better control but lower running costs too, and therefore also reducing your carbon footprint.
Coupling SmartSola™ with our unique SmartStor™ control system, which already gives you complete control of your storage facilities with anytime and anywhere communication via a phone, tablet or computer, the ability to collect store performance data and knowledge across multiple platforms and now also give you potentially huge cost savings too.
“To help achieve NetZero by 2050 the industry must look at using energy far more efficiently using more sustainable sources whilst minimising crop deterioration. Automation of store monitoring and control systems will play a big role in reducing energy usage.
SmartStor™ controls all aspects of storage and allows fine tuning of equipment. In conjunction with our new SmartSola™ module we distribute the energy you produce from alternative sources such as Solar and Wind Power to prioritise your store needs and when coupled with good store design reduces the reliance to buy energy thus reducing your carbon footprint.”
THE FUTURE OF UK POTATO STORAGE RESEARCH
Ray Andrews, Managing Director of Crop Systems Limited, wrote the following letter to all major UK farming press outlets on April 24th, regarding the future of Sutton Bridge Research Station, because he felt too few people in the industry were addressing the future of this unique facility:
AHDB’s announcement that it is consulting on the future of the Sutton Bridge Crop Research Station, and on potato storage research more broadly, should worry every potato grower in this country.
Too many people in the sector still seem unaware this is happening, so we risk sleep-walking into an uncertain future.
The excellence of Sutton Bridge’s work is recognised right around the world.
Since it was launched in 1964 it has built up an outstanding track record for world quality research. It is a jewel in the crown that should be treasured rather than trashed.
Completing all major research into such a complex subject on one site means it has a unique synergy and level of co-ordination that cannot be achieved if the work were split between multiple sites, no matter how excellent those individual sites may be.
In addition, this proposal comes when growers are facing a unique triple threat; from coronavirus; from the withdrawal of CIPC and from Brexit.
The last thing it needs is uncertainty hanging over a unique, world-leading research facility that has achieved so much.
I urge everyone involved in the potato industry to make their voice heard and to protect this unique facility.
Ray Andrews, Crop Systems Limited
SMARTSTOR® GETS SMARTER
Crop Systems Limited is adding new features and improved functionality to its SmartStor® controller, which will help users reduce storage costs, while improving their ability to monitor and manage stores remotely via mobile devices.
New features include a heating/drying system, a power control feature that avoids store equipment running at peak energy prices, two independent energy saving programmes and an ethylene control feed system that reduces loss of this sprouting suppressant during purging and ambient cooling.
The new SmartStor® control system also features a new selection and graphing element that enables store operators to select which parameters they need to monitor to manage their stores remotely, as well as a new interface.
It then displays these figures on an easily read graph, so they can track them in real time in a form that can easily be read on any mobile device or computer, says Ray Andrews, Managing Director of Crop Systems Limited:
“This system enables users to concentrate on the information they really need without being diverted by any other data, but secure in the knowledge that it is all being recorded should it ever be needed”.
All the features are being introduced in response to user feedback, he says: “The heating system is being introduced in response to requests from customers who need to dry wet crops and cure them quickly before they go into long-term storage.
“With energy prices varying widely – and the charging periods used by energy companies changing regularly – other customers told us they need to optimize use of lower-cost energy, and particularly to avoid running major equipment operating automatically during ‘peak rate’ periods.
“The new feature will avoid that by turning all equipment off when those key high-cost energy periods occur, and turn it back on when costs are lower.
“With ethylene increasingly being used as a sprouting suppressant, another new feature turns supplies off during store purging and ambient cooling, which will reduce wastage. That system also includes a CO2 accumulator, so operators will have a complete record of their crop’s accumulated CO2 exposure”.
The new SmartStor® will be demonstrated live on Crop Systems Limited’s stand (No 115) at British Potato.
TAKE COMPLETE CONTROL
Potato store operators need to take complete control of their stores to ensure the crop they present to their customers is as close to ‘just harvested’ condition as possible.
But achieving that can be harder than it at first seems, says Ray Andrews from Crop Systems Limited, because the potato harvest and crop cooling period clashes head-on with autumn field work:
“There is always a danger that – if checking on potatoes is part of your daily tasks – it will get neglected if something unexpected crops up, such as the main cultivating tractor breaking down or some grain needs loading out.
“If your crop suffers damage at this stage it is an expensive loss because all the costs of planting, growing and harvesting have already been incurred.
“The only situation that is worse is if it comes out of store in unmarketable condition due to poor store practice, because then you can add the storage costs to that bill”, he says.
“This was one of the main motivations for Crop Systems Ltd launching the SmartStor ® controller, which enables operators to monitor and manage their stores remotely.
“It means that, even if you are very busy on other tasks, via a combination of the alarm and management features in the system your retain complete control of the store and the valuable crop it contains.
“Quite apart from the financial advantages of that, it also offers you complete peace of mind”.
In many cases he suggests operators can significantly improve the operational efficiency of their stores without having to make significant investments:
“The priority has to be to ensure that all machinery is operating efficiently, both in terms of how it controls the store and in terms of energy usage.
“If it is not operating efficiently the crop will still be at risk, and storage costs could be considerably higher than they need to be”.
The impending loss of CIPC as a sprouting suppressant makes efficient store operation all the more important, he adds, with the debate around its impending loss helping focus minds on the storage issue:
“If a store is already CIPC compliant then the chances are it is efficient. Stores that failed to meet application limits might not be failing on that level alone; they probably needed significant improvement anyway.
“And if they are already efficient the loss of CIPC will not be as serious an issue as we might at first think, because whatever treatment growers use in future will be used efficiently”.
Losses in store are just part of an overall wastage in potatoes – quoted as being between 25% and 30%.
These start with greening in the field; damage and losses at harvest and during handing; and include rotting and damage caused by disease or nutrient deficiencies:
“Rotting is a real problem. If you react quickly you can minimize the damage caused; but if you do not spot it quickly it can spread to healthy adjacent potatoes and lead to significant losses.
“We can minimize the damage caused by issues like shrinkage by using treatments like humidity”.
The industry will always have to grow an extra percentage of crop, Ray believes, simply because growers have to ensure they meet their contracts and give themselves some leeway in case of problems during the growing cycle:
“The real key to efficiency is not to lose any part of the crop you already grow by not following best practice at all stages of the production cycle.
“And bear in mind that one of our customers managed to store October 2017 harvested potatoes for over 13 months in a new store: that is what you can achieve if you get it right”.
EFFICIENT ENERGY USE KEY
Many potato store operators are missing out on the chance to make significant savings in energy costs because they don’t have enough information on their energy usage to make informed decisions.
Yet using some simple technology – as either original or retro-fit – would enable them to make the right move, says Ray Andrews, from Crop Systems Limited:
“I don’t think many operators realise how much energy prices vary, or how frequently in any 24 hour period they change. Bear in mind that peak energy prices are often three times higher than off-peak rates.
“And these things are not fixed. I am sure many people don’t know how frequently suppliers change their pricing structures and timings. What represents the best deal today might not represent the best deal next week.
“Unless you keep a constant eye on everything – or use a store controller that does that job – you risk missing out on the best prices and the lowest available storage cost.
“This was one of the priorities we set in developing the SmartStor control system”, says Ray.
“This allows you monitor and manage your store 24-hours a day, even when you are away from it. That includes enabling you to monitor the best energy prices and store fan/fridge running times.
“I have great sympathy with farmers as they try to find the most competitive energy supplier. You might assume that your local farmer co-operative would give you the best price, but we have worked with farmers paying 13.5% less by dealing direct with the energy company.
“Our advice would be to look beyond the headline ‘unit cost’ and work out the cost including things like the capacity charge, renewal obligation, feed-in-tariff, reactive power charge, forecast charge, operational charge, data collection charge, administration, and climate levy.
“Having that day-to-day control is now imperative, and via SmartStor we can tell you your costs to the nearest penny minute by minute, calculate how the multiple tariffs charged can best be exploited to your advantage and give you complete control over your store”.
While the controller is key, it is also important to make sure the parts of the store equipment that consume energy are working efficiently:
“Let’s start with the fans, which are crucial to move the air through the crop and the store.
“Fans come in all shapes and sizes and generally push out a set quantity of air for every kw of power used – that is great if they are the correct size for the job in hand; but bad news if they are not correctly sized.
“In our experience, grain fans used in potato stores can consume 35% – 40% more energy than correctly sized fans that are designed for the job. And always remember than new fans are likely to be far more efficient than old ones.
“They also need to be correctly matched to the ducts and laterals used in a bulk store, or the pressure in them may rise to above the fans’ characteristics.
“While you need high capacity fans to dry and cure crops – or to blast them if they come in wet – the key to efficient energy use is to know how far you can slow them down at other times of the year.
“If fans are run at 80% of their capacity they use half the energy the do when running at full speed. The savings reduce when they run at lower speeds – but at that stage it is more important to ensure you are achieving the required airflow to maintain efficiency”.
Recirculation is essential to maintain performance, he adds. If airflow is insufficient then the air will not move through the crop effectively, while too much movement risks wasting energy and may also risk increasing dehydration.
Most operators are now using CO2 purging to counter conditions like Blackheart, but they need to be sensible about the levels they use. If they try to reduce it to 1,500ppm it consumes a huge amount of energy. Even moving from higher levels – 3,500ppm to 4,500ppm – makes a huge difference.
Similar issues affect fridges, with poorly performing units often using double the energy of efficient ones, while still struggling to achieve the same effect.
If the coil temperature is too low it can trigger a succession of problems – starting with fans having to run longer than ideal; the potential for premature icing which may restrict airflow; air short circuits and expansion valves shutting.
Once problems start they can build up rapidly, and de-frosting simply puts in-wanted heat back into the store and uses more energy. Installing as control system that enables you to keep a constant eye on problems like this – and which also sends you an alarm message as soon as the problem is detected – makes good sense, both in terms of keeping your stored crop in best condition and in terms of controlling storage costs.
Another key asset is being able to harness humidity with adiabatic cooling, which while it has limitations can have a serious impact on reducing energy usage.
Mr Andrews recently led an Innovate UK funded industry project examining the efficiency of box stores which showed that suction chambers can help improve air flows by up to 65%. Even greater improvements were achieved by the addition of other features such as plenum walls and side/top sheets.
CROP SYSTEMS LIMITED EXPANDS
Crop Systems Limited is starting 2019 in new purpose-developed premises that will enable it to continue expanding its business.
The company, founded over 20 years ago by Ray Andrews, is renowned for its innovative, market-leading range of technology and products and is growing quickly due to their success.
The new factory at Happisburgh, Norfolk was previously two separate units which have been combined into one integrated 15,500 square foot factory which offers ample open plan space for all stages of the company’s manufacturing activities and for parts storage.
In addition a new two storey set of offices, meeting and training rooms has been added to bring all parts of the company together in one unit.
Crop Systems Limited now employs 22 members of staff, and is enjoying a significant rise in business thanks to its latest innovations, says Mr Andrews:
“The company’s low TD In-Line refrigeration units and Humidity Systems has proved successful in offering farmers and sore operators low energy costs and minimal weight loss.
“The Smart Stor controller has been a huge success and is proving highly valuable when replacing controllers of all other makes, with the latest Innovate trials on improving air flows in store leading to fresh orders.
“We believe moving to the new factory – combined with a continued effort to build our team and our sales – will help the company grow healthily in the future”.